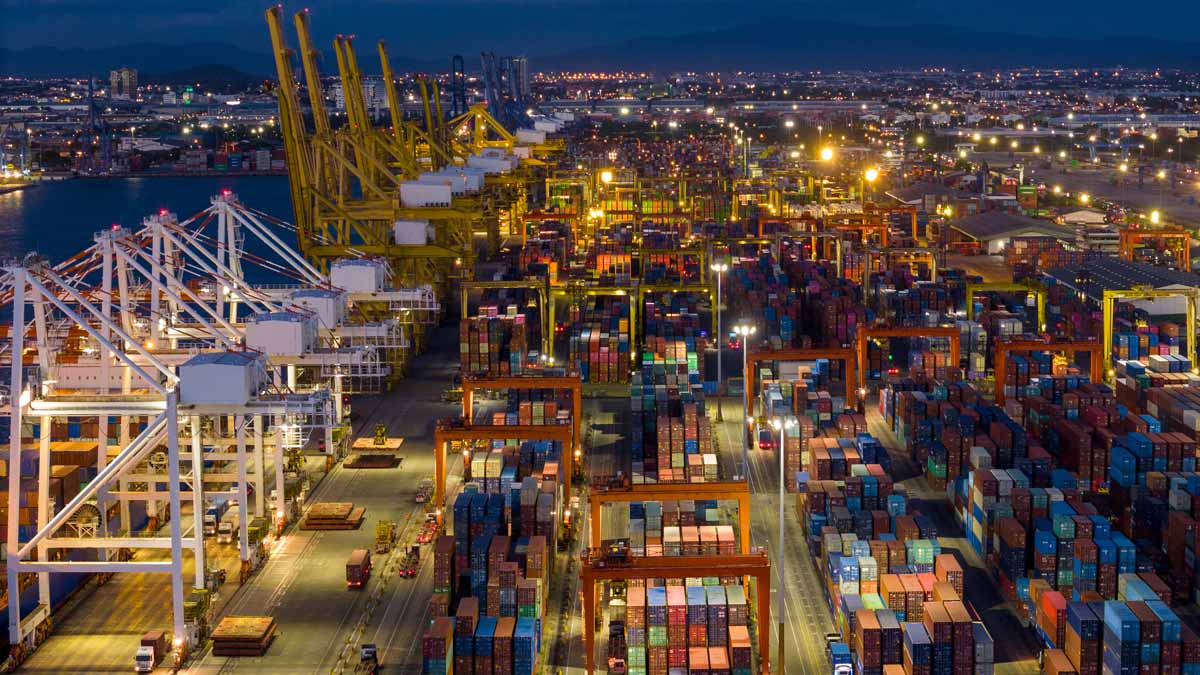
Every third shipping container is transported empty. That’s 60 million empty container moves a year. The process of moving empties or ‘repositioning’ costs the shipping industry more than $20 billion annually. As the manager of a container carrier, leasing company, or logistics firm, you are likely aware that it can represent up to 8% of total operating costs.
In light of these costs, the question of how to achieve more efficient shipping container movement is on everyone’s mind. World trade relies heavily on the timely transport of goods, so even minor inefficiencies in container handling can ripple into costly delays and bottlenecks.
As supply chain networks grow increasingly complex, adopting a systematic approach to container management is crucial to maintaining cost efficiency and operational fluidity. Today, we’ll break down how to optimize shipping container movement.
Meticulous Planning and Forecasting
Meticulous planning and forecasting are the keys to improved shipping container movement.
In recent years, converging data and logistics have paved the way for enhanced predictability and operational control. By incorporating predictive technologies, supply chain stakeholders can proactively address challenges such as fluctuating demand or unexpected disruptions.
For example, terminal managers can use historical data to apply predictive analytics to anticipate container demand and identify peak activity periods. Understanding traffic patterns and integrating this data with arrival schedules helps decision-makers pre-plan container placements to reduce unnecessary moves within the yard.
Moreover, optimizing yard layouts to accommodate different cargo types or container sizes allows for smoother operations and reduces dwell time. When schedules align with yard planning, the reduction in manual repositioning significantly lowers costs and enhances efficiency.
Combining these elements ensures that every action within the terminal yard contributes to a streamlined operation.
Real-Time Visibility Through Technology
Incorporating technology for real-time tracking is no longer a luxury—it’s a necessity. GPS and IoT-enabled sensors provide unparalleled transparency, enabling operators to monitor container movements across their supply chain. Real-time updates ensure deviations from planned schedules—such as delays or congestion—are promptly identified and addressed.
Automated alerts play a critical role here, informing stakeholders of potential disruptions before they escalate. This minimizes downtime and fosters improved coordination among transport providers, terminal operators, and other key players. Integrating ERPs and TOSs allows data to be accessed in a single source of truth and delivered within existing workflows.
Automation and Integration Across the Supply Chain
Automation promises a number of breakthroughs for the container shipping industry.
Technologies like automated cranes, yard trucks, and guided vehicles (AGVs) have introduced consistency and speed into traditionally manual processes.
Cranes, in particular, can execute repetitive tasks with pinpoint accuracy, reducing the likelihood of errors and ensuring faster container turnover. However, no matter how advanced the technology or comprehensive the planning, collaboration across the supply chain remains vital for optimal container movement. Ensuring smooth communication between shipping lines, port authorities, and trucking companies can eliminate inefficiencies and speed up turnaround times. Integrated systems are the key to this.
For instance, when terminal operators share real-time container availability updates to trucking companies, trucks can be dispatched at optimal times, reducing idle time at the terminal delays and ensuring more efficient pickups and deliveries. Similarly, integrating shipping line schedules with terminal operating systems enables better resource allocation. Unified platforms save time and foster stronger partnerships across the supply chain, driving collective success.
Driving Efficiency Through Constant Innovation
Operators should regularly evaluate their processes and invest in emerging technologies aligning with their goals. For example, machine learning (ML) algorithms are increasingly being used to predict maintenance needs for automated equipment, reducing unexpected downtimes further.
The UN has warned that shipping is the source of up to 3% of worldwide greenhouse gas (GHG) emissions. It’s no surprise that the race towards greener terminals is underway, with some operators exploring on-site renewable energy generation to power yard equipment. It’s necessary, as terminals are extremely power-intensive.
Electrified equipment and smart route optimization are already helping to reduce environmental footprints. Macgregor now sells 24/7 electric trans-loading terminal cranes (with a 50t safe working load) that use around 60% less energy than their hydraulic equivalent and has received orders from PT Karya Teknik Utama for its Indonesian shipyard.
Yokohama Port in Japan, ranked 9th on energy efficiency by CPPI, is developing facilities to store and use green methanol for its shipping fleet. These sorts of eco-conscious initiatives should help satisfy looming regulatory requirements and raise brand reputation in an era of heightened environmental awareness.
Another way to boost yard efficiency is to prioritize professional development, equipping your employees with the necessary skills and confidence to operate at peak precision. Always remember that your people are your greatest asset.
With the help of terminal operating solutions from Tideworks Technology, you can eliminate outdated, time-consuming manual processes, fragmented data, and limited visibility. Such challenges were once unavoidable in the supply chain—but are fast becoming relics of the past.
Learn more about how our software solutions can optimize container operations. Contact us today.